Plastic extrusion for thermoplastics, PVC, and engineering plastics
Plastic extrusion for thermoplastics, PVC, and engineering plastics
Blog Article
A Comprehensive Guide to the Refine and Advantages of Plastic Extrusion
In the vast world of manufacturing, plastic extrusion becomes a highly effective and crucial procedure. Transmuting raw plastic right into constant profiles, it provides to a myriad of markets with its remarkable adaptability. This overview intends to illuminate the complex steps included in this method, the kinds of plastic apt for extrusion, and the game-changing benefits it gives the industry. The occurring conversation guarantees to unfold the real-world effects of this transformative procedure.
Understanding the Fundamentals of Plastic Extrusion
While it might appear facility at initial look, the process of plastic extrusion is basically straightforward. The procedure starts with the feeding of plastic material, in the type of pellets, granules, or powders, into a warmed barrel. The designed plastic is then cooled, solidified, and reduced into desired sizes, finishing the process.
The Technical Refine of Plastic Extrusion Explained

Kinds Of Plastic Suitable for Extrusion
The selection of the ideal type of plastic is a crucial element of the extrusion procedure. Numerous plastics supply distinct residential or commercial properties, making them extra fit to specific applications. Polyethylene, for instance, is generally made use of because of its affordable and easy formability. It supplies excellent resistance to chemicals and moisture, making it perfect for products like tubing and containers. Polypropylene is another prominent option due to its high melting point and resistance to fatigue. For even more durable applications, polystyrene and PVC (polyvinyl chloride) are often chosen for their toughness and durability. These are usual alternatives, the option ultimately depends on the details needs of the item being created. Recognizing these plastic kinds can dramatically improve the extrusion process.
Contrasting Plastic Extrusion to Other Plastic Forming Approaches
Recognizing the kinds of plastic suitable for extrusion paves the means for a broader conversation on how plastic extrusion stacks up versus other plastic forming techniques. Plastic extrusion is unmatched when it comes to creating continual accounts, such as pipes, seals, and gaskets. It also permits for a regular cross-section along the size of the item.
Key Benefits of Plastic Extrusion in Manufacturing
In the realm of manufacturing, plastic extrusion provides several substantial benefits. One noteworthy advantage is the cost-effectiveness of the procedure, that makes it an economically enticing manufacturing technique. Furthermore, this method provides superior item flexibility and enhanced manufacturing rate, consequently raising total production efficiency.
Cost-efficient Production Technique
Plastic extrusion leaps to the forefront as an economical manufacturing technique in production. This procedure attracts attention for its ability to generate high quantities of material promptly and successfully, offering suppliers with substantial cost savings. sites The primary price advantage is the capability to make use of cheaper resources. Extrusion uses thermoplastic products, which are less expensive contrasted to steels or porcelains. Better, the extrusion procedure itself is relatively basic, decreasing labor expenses. Furthermore, plastic extrusion requires much less energy than standard production approaches, adding to lower functional prices. The procedure additionally reduces waste, as any type of faulty or excess materials can be recycled and reused, giving an additional layer of cost-effectiveness. In general, the economic advantages make plastic extrusion a very attractive choice in the production industry.
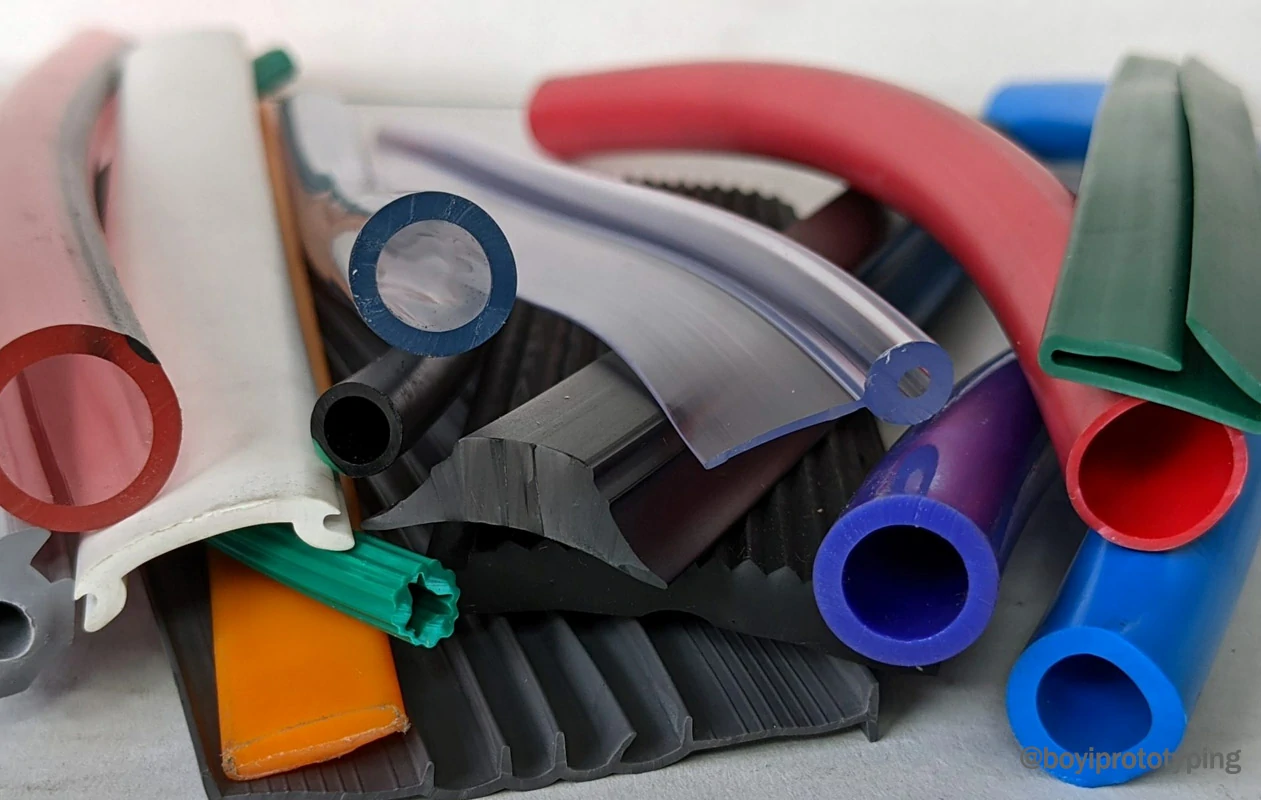
Superior Product Flexibility
Past the cost-effectiveness of plastic extrusion, another significant advantage in producing hinge on its superior product versatility. This procedure allows for the production of a vast variety of items with differing shapes, styles, and sizes, from straightforward plastic sheets to detailed accounts. The flexibility is connected to the extrusion die, which can be personalized to yield the preferred product design. This makes plastic extrusion a suitable solution for sectors that need customized plastic elements, such as automotive, building and construction, and product packaging. The ability to produce varied products is not just advantageous in meeting certain market demands however also in allowing producers to explore new product with minimal resources investment. Fundamentally, plastic extrusion's item adaptability fosters development while boosting operational efficiency.
Enhanced Production Speed
A considerable benefit of plastic extrusion exists in its enhanced manufacturing rate. Few other manufacturing procedures can match the rate of plastic extrusion. Additionally, the ability to maintain regular high-speed production without sacrificing product quality establishes plastic extrusion apart from various other techniques.
Real-world Applications and Effects of Plastic Extrusion
In the realm of manufacturing, the strategy of plastic extrusion holds profound relevance. This procedure is extensively made use of in the production of a range of products, such as plastic tubing, window frames, and climate stripping. As a result, it significantly influences sectors like building and construction, packaging, and automotive industries. Its influence prolongs to everyday products, from plastic bags to toothbrushes and disposable cutlery. The financial advantage of plastic extrusion, mostly its high-volume and cost-efficient outcome, has actually reinvented production. The ecological effect of plastic waste continues to be an issue. The market is constantly making every effort for innovations in eco-friendly and recyclable materials, indicating a future where the benefits of plastic extrusion can be preserved without jeopardizing ecological sustainability.
Verdict
To conclude, plastic extrusion is a efficient and highly efficient technique of changing resources right into varied products. It offers various advantages over other plastic forming methods, consisting of cost-effectiveness, high outcome, very little waste, and design versatility. Its influence is exceptionally felt in various sectors such as the original source building, vehicle, and durable goods, making it a pivotal procedure in today's manufacturing landscape.
Digging deeper right into the technical procedure of plastic extrusion, go to this site it begins with the option of the ideal plastic material. Once cooled down, the plastic is reduced into the needed sizes or wound onto reels if the item is a plastic film or sheet - plastic extrusion. Contrasting Plastic Extrusion to Other Plastic Forming Methods
Understanding the kinds of plastic suitable for extrusion paves the method for a broader conversation on how plastic extrusion piles up versus other plastic forming techniques. Few various other manufacturing procedures can match the speed of plastic extrusion.
Report this page